Industrial Automation could be the best possible option as the solution to such challenges mentioned above. It helps boost the product quality, reliability, and production rate, on the one hand. At the same time, on the other hand, it reduces production and design costs by adopting new, innovative, and integrated technologies and services.
In such a scenario, the market stats have much to tell… as brought about by the Markets and Markets; it could be noted that the global industrial control & factory automation market size is anticipated to score USD 197.8 billion by 2026. This growth is projected at a CAGR of 8.2% from a predicted USD 133.1 billion during 2021.
While the market specs look good, let’s take a note at what are the driving forces behind it –
- The advent of connected enterprises, alongside the need for mass manufacturing.
- Constant initiatives by governments to foster industrial automation.
- Industrial environments stance of widely adopting technologies like IoT and AI.
- High emphasis on optimum utilization of resources
- Importance of industrial automation and maximum utilization of means, devices, and fiscal policies formed by local financial institutions to retain manufacturing facilities surviving amidst the COVID-19 crisis.
Better explanation of the Industrial Automation arena could be understood with the help of its advantages, which are as below –
- It serves to render bulk and large-scale production by effectively lessening assembly time per product with more exceptional quality of production.
- Synthesis of multiple processes in the industry with automated machinery lessens cycle times and effort, subsequently reducing the human labor demand.
- It would help adapt and monitor the industrial processes in all stages, right from the inception to the end of product, fostering uniformity and product quality with higher compliance.
These advantages help the various industrial processes automatically adapt to the process variables as per the set/desired values utilizing closed-loop control techniques. Though complex in nature, provided the large number of devices associated, Industrial Automation could prove very useful if the hierarchical arrangement is followed. Let’s take a look at the different hierarchical levels of the Industrial Automation system –
Field Level
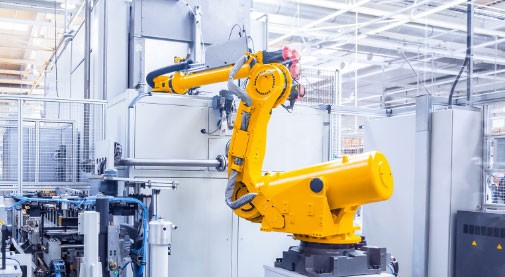
Being the lowest level of the automation hierarchy, Industrial Automation includes field devices such as sensors and actuators. With the main agenda to transfer processes’ and machines’ data to the next higher level for monitoring and analysis, field devices also contribute to controlling the process parameters.
While sensors convert real-time parameters into electrical signals, actuators, on the other hand, convert the electrical signals into mechanical means to control the processes. Initially, real-time parameters such as temperature, pressure, flow, level, etc., are monitored and analyzed by the controller, to which the sensor data is also conveyed.
A few instances of sensors could be a thermocouple, proximity sensors, RTDs, and flow meters. In contrast, Flow control valves, solenoid valves, pneumatic actuators, relays, DC motors, and servo motors are examples of actuators.
Control Level
The Control Level helps one fetch the process parameters through varied sensors with the help of different automation devices including PLCs, CNC machines, and more. These automatic controllers use both the processed sensor signals and control techniques to ultimately drive the actuators.
One of the most widely used industrial controllers that deliver automatic control functions based on input from sensors is Programmable Logic Controllers (PLCs). And, it comprises different modules such as CPU, analog I/O, digital I/O, and communication modules. Moreover, at this stage, it’s all about the controller devices facilitating the operator to program a control function or strategy, thereby also allowing the performance of a certain automatic operation on the process.
Supervising and Production Control Level
This stage brings in the automatic devices and monitoring systems that allow the controlling and intervening functions such as HMI, alongside supervising various parameters, setting production targets, historical archiving, setting machine start and shutdown, and much more. HMIs like Distribution Control System (DCS) or Supervisory Control and Data Acquisition (SCADA) are usually employed at this level.
Information or Enterprise Level
Known as the top level of industrial automation, this stage is all about managing the automation system through tasks such as production planning, customer and market analysis, orders and sales, etc. This level, hence, majorly deals more with commercial activities rather than the technical aspects.
Apart from these, the Industrial Automation systems work on industrial communication networks that provide a continuous flow of information across the chain. A few of these networks could be named as RS485, CAN, DeviceNet, Foundation Field bus, Profibus, etc.
From the information displayed above, we can conclude that there’s a constant data flow through and at all the levels. It could be noticed that the information gets aggregated when at the sensor level, while at the top/server/enterprise level, one gets detailed information regarding all the processes.
We, at Teksun Inc, foster complete knowledge when it comes to Industrial Automation. Wish to know more about Industrial Automation and how it could bring a progressive transformation to your business!? Connect with our team of professional experts, and take your first step towards beating your competitors…