Five important advantages of IoT-driven predictive maintenance are listed below:
Extension of Equipment Life
While a combination of quantitative and qualitative measures has typically been used to anticipate issues and save downtime, predictive maintenance can successfully help businesses extend the useful life of their equipment. Companies can gain a thorough understanding of the health of their equipment by using real-time data from IIoT sensors generated on the production line and equipment to prioritize, schedule, and optimize repairs for improved performance. Teams can fix any problem before it gets out of hand and maintain equipment operating at its best for longer by anticipating potential failures before they happen.
Increasing Production Quality
Predictive maintenance implementations had a positive ROI in 83% of the cases, and 45% of those polled showed amortization in less than a year, according to a recent study in the industrial sector. This is because predictive maintenance systems can identify mistakes as they occur. Issues that affect overall productivity, such as expenses, downtime, and safety concerns, can be handled proactively to reduce their impact on enterprises. Maintenance teams may operate at their most effective level by scheduling maintenance in advance rather than reallocating their resources to fix broken equipment. Problems can be solved while enhancing overall performance thanks to IoT systems’ consistent data and frequent, rapid process modifications.
Lowering maintenance costs and downtime
In this sense,IoT predictive maintenance’s developing condition will enable operators to be more proactive in spotting equipment defects. Historical data obtained from various IoT devices and sensors can offer valuable metrics on machine health, usage, and risk areas for sectors that rely heavily on equipment. Predictive AI-powered models can assist in developing frameworks that fill in the gaps in the absence of complete historical data by replicating actual use cases. The amount of money spent and the amount of downtime experienced can be significantly reduced when action is planned around the data gathered.
Finding the Inefficient Areas
Modern algorithms and sensor data analytics can more accurately provide leads when it comes to equipment. Real-time, immediate insights are essential for identifying inefficiencies as soon as possible and can even be used to enhance systems as needed. For instance, a power firm may discover new ways to enhance its production grid and reap higher advantages thanks to the data insights from an IoT-based sensory framework supported by AI solutions. Additionally, it is possible to identify potential safety concerns, dangerous circumstances, and compliance problems and take the necessary mitigation measures.
Quicker and Better Decision Making
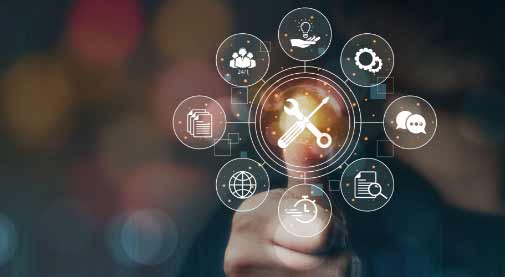
IoT devices can serve as real-time data providers anytime, everywhere, thanks to their interconnections. The cherry on top of predictive maintenance is the ability to act swiftly and intelligently from any location. Manufacturing analytics and sensor data insights give managers a clear image of flaws, potential improvement areas, and other important performance markers.
In the future, any corporate software will have to include predictive maintenance as a mandatory requirement. Companies will need to ensure that they have a solid data architecture to go along with powerful machine learning models, though, to guarantee that the solution is dependable. In an industrial setting, there are countless data sources. A company’s future competitive advantage will greatly depend on developing strong data processing capabilities at the location where data is being collected.
IoT and predictive maintenance integration
We can precisely forecast issues with equipment and assets thanks to multi-technology and system integration. One of the most powerful technologies, the Internet of Things, enables businesses to pinpoint all problems and take appropriate action.
The IoT network can be employed with a wide range of technologies, apparatus, and systems to develop a predictive maintenance program. These consist of the following:
Data communications:
Using the required communication tools, data is transported to central storage as sensors collect data and actuators translate it. An organization can either set up an internal or a public cloud storage system.
Sensors:
There are many different sizes and shapes of sensors. They can be used to gather information. They are placed at certain locations, points, and positions within assets.
Predictive maintenance software:
The data analysis program in question is this one. It is in charge of producing reports using the supplied data. Users may receive notifications regarding machine usage, including a warning if the asset exceeds the user-defined limits.
Data Storage:
This can be a server or cloud storage where all the data is kept for further examination. Predictive analytics systems can extract these data for analysis and transformation into understandable information.
Predictive Analytics:
Predictive analytics solutions enable actionable insights once the data has been understood and are powered by machine learning.
Takeaway
The Internet of Things, predictive analytics, and maintenance systems revolutionize business processes. They offer the effectiveness and precision companies need to achieve maximum performance in all areas. Manufacturers can use IoT predictive maintenance solutions to boost output while utilizing current resources and personnel.
Can you be more specific about the content of your article? After reading it, I still have some doubts. Hope you can help me. https://accounts.binance.com/it/register-person?ref=DB40ITMB