This is simply the tip of the iceberg regarding the amazing possibilities that industry 4.0 solution has to offer. The Industrial Internet of Things (IIoT) is a disruptive force that will affect product development patterns in the next decade and beyond.
What exactly is the Internet of Things (IoT)? It only fits that, Wikipedia provides one of the clearest definitions: “The network of physical objects—devices, vehicles, buildings, and other items embedded with electronics, software, sensors, and network connectivity—that enables these objects to collect and exchange data. It allows objects to be sensed and controlled remotely across existing network infrastructure, creating opportunities for more direct integration of the physical world into computer-based systems, and resulting in improved efficiency, accuracy, and economic benefit.”
It’s evident that when it comes to IIoT market adoption, we’re still in the early phases of understanding and acceptability. According to a recent poll, 13% of industrial engineers are currently implementing IIoT solutions, and another 22% are exploring experimental projects. Analysts predict that by 2025, robots will do 25% of all manufacturing, and the IIoT will connect 50 billion gadgets.
IIoT will be much more than a buzzword for today’s industrial product designers. It can easily and cost-effectively connect every factory floor component to the network. This capacity will allow for considerable improvements in product performance and cost-of-ownership reductions—factors that will have a big impact on a product’s market value and profit margin.
The Five Design Possibilities
Five logical areas for IIoT integration arise as an industrial machine and component designers begin product development. Are you considering these possibilities as part of your product strategy?
Remote Access and Monitoring
Today’s industrial machinery produces large amounts of diagnostic data. However, getting this information in a meaningful way can be difficult. Connecting devices and accessing their user data frequently necessitates prohibitive levels of commissioning and integration.
Remote access to machine data down to the device level is possible because of a mix of web-based technologies, networking, and software. Designers will provide maintenance technicians, control engineers, and plant managers with simple access to diagnostic information, whether at the plant, at the office, or home, thanks to the IIoT solutions.
Analytics and Optimization
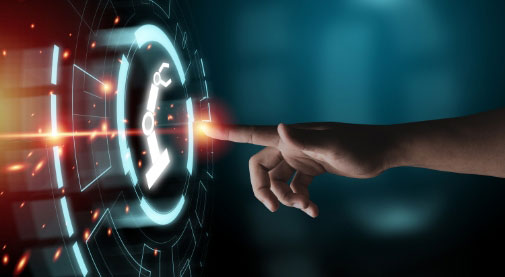
To avoid downtime, plant operations must know when the best time is to undertake machine maintenance. Maintenance professionals can spot performance variations that indicate a problem. Analyzing specific performance trends might reveal whether a machine part has reached its limit or has been constrained, necessitating service.
Production equipment designers can use multiple software platforms to provide predictive maintenance, historical and current diagnostics, and tune control, thanks to the continuously dropping cost of sensors and wireless networking. The machine can use this feature to notify a person or system that maintenance is required.
Designers can use the available data to deliver cost-effective machine analytics and optimization, reduce production downtime, and better utilize limited maintenance resources, thanks to the IIoT solutions. Because commissioning and troubleshooting are expensive, key tasks are simplified by easy access to comprehensive, automated diagnostic web pages that are simple and intuitive.
Users may quickly do a self-test, view real-time network/error information, and log numerous diagnostic events, such as low- and high-voltage alerts, using this technology.
Web-based diagnostic tools allow you to diagnose problems from anywhere in the world.
Consumption of energy
Due to significant cost reductions in sensor, wireless, and microprocessor technologies, designers will be able to regulate energy in manufacturing machines in ways that were previously uneconomical. A production machine can be configured to learn its operating practices and considerably reduce energy use, similar to the modern “learn” thermostats.
Designers can limit power consumption by leveraging a machine’s diagnostic and control functions with optimization algorithms and audits. Furthermore, the ability to program logic and intelligence into a machine allows it to power up and down or fully shut off if it is idle.
Improved Asset Reliability
A valve fires, a cylinder moves, and a bearing turns thousands of cycles per day on a production machine. With IIoT solutions, it is economically feasible to monitor these moving parts. Armed with this information, it is possible to determine if the devices are functioning within normal tolerances or if their performance is degrading to the point of failure. This capability is known as “prognostics.”
Prognostics meets the promise of predictive maintenance for substantially improved asset reliability in a cost-effective manner. Designers can now incorporate the ability to forecast a machine’s performance and maintenance needs. For example, depending on assessed performance decline, the engine can warn you that there’s a higher chance of device failure soon. You may make the equipment to notify the user when it fails and sends an automated message to the manufacturer or distributor if a replacement part is needed.
The Internet of Things (IIoT) and prognostics are transforming asset management and maintenance methods. Rather than wasting time and money on unnecessary preventative maintenance or waiting until a machine breaks down and loses productivity, the device can send out an “I need to be fixed” warning and, in the future, repair itself. There is no downtime in production, and maintenance is only done as needed.
Legacy Equipment Retrofitting and Virtually Infinite Lifecycle Design
Many manufacturing machines have a 20-year life expectancy. Their longer service lifecycles highlight two major concerns: What can designers update older equipment with IIoT features at a low cost? And, more importantly, how can designers create machines with virtually endless lifecycles that outlast the customer’s requirements?
Sensor, software, and relatively inexpensive network technologies can add significant value to existing equipment. If an OEM has a big installed base, it should consider manufacturing kits that enhance machine capabilities while also extending its service life. A computer-numerical-control (CNC) machine’s programmable logic controller (PLC) protocol, for example, might be changed to connect to a factory Ethernet network. This will unlock the machine’s data and enable plant-wide information aggregation.
If a new product is being developed, the designer should use IIoT technology and industry 4.0 solution to maximize its lifecycle. This entails giving the user the ability to upgrade the system cost-effectively regularly. Hardware should handle future software upgrades, and network protocols and standards should allow for plug-and-play functionality.
Three Foundational Design Considerations
Developers must consider three design concerns when incorporating IIoT capabilities into their devices.
The first and most important consideration is security. Theft of well-publicized financial and personal data pales compared to the devastation that may be done by compromising control systems in industrial, refineries, and power plants. As the IIoT allows for greater control over the actual world, the attention must shift to multi-layered security. To reap the benefits of IIoT, this problem must be resolved.
The second concept is interoperability and modularity, which means that components and machines must communicate and work together easily. Devices should be modular and plug and play on a network, requiring little configuration and commissioning. That includes implementing higher-level standards that make it simple for machines to communicate with one another.
Finally, real-time functionality propels users of equipment forward into the future. This is the difference between driving while glancing in the rearview mirror and driving while looking forward through the windshield. It informs consumers about what is happening in their machines right now and, more crucially, what will happen tomorrow. “I’m starting to observe delays in how a spool is shifting in a valve,” a piece of industrial equipment might say. It will most likely collapse in 90 days. As a result, we’ll have to place an order for parts.” With the IIoT solution, such a capacity is achievable.
Summary
Machine designers will gain access to a slew of new capabilities thanks to IIoT solutions. Their OEM products will gain substantial value and a competitive advantage as a result of their efforts. However, designers must consider how their equipment will fit with the new IIoT world.
To meet the increased software requirements that lie ahead, sturdy hardware, adequate processing power, and sufficient memory will be required. Furthermore, to send data to higher-level networks for asset-management applications, machines must comply with the most current standards.
To create goods for the emerging IIoT environment, designers should follow these procedures.
End-user customers will benefit from easier equipment commissioning at a cheaper cost, thanks to the IIoT. Asset management at the factory level will become possible and cost-effective. As prognostics become a reality, the promise of predictive maintenance will be realized. Customers are more accepting of IIoT, and they are willing to pay a premium for items that contain its benefits.