The Premise
Machine Monitoring is not a brand-new concept in Industry 4.0, but it seems to have very well seeped into the market now. Why are we discussing it here? Well, that’s because Machine Monitoring is way more than what businesses understand. Right from an array of benefits to ease of carrying out substantial tasks to staying available for a range of applications, Machine Monitoring stands for all. Let’s question our way to find the right solutions beneficial for your business…
What Are The Fruits Born By Machine Monitoring?
Before considering the fruits of Machine Monitoring, we may rightly know that it is a useful and practical concept for both discrete and process industries. The coming times have made Machine Learning more affordable, provided that the sensors have grown more economical. Moreover, it could be witnessed that on one side, where the Edge Devices have become more versatile, the connectivity provisions, on the other hand, have become more robust. This calls for enhanced and sprawling parameters to track, as well as more opportunities to create value than ever before.
Accurate Performance Measure:
Firstly, with the edge of automation, it could be known that Machine Monitoring could establish more accurate performance measures, which in the case of manual measurements would be prone to errors and deviations.
Real-Time & Quick Notifications:
Machine Monitoring allows you to automatically notify your manager/technician if a set threshold is crossed, and that too by easily configuring your solution to the system.
Systematic Maintenance:
The featured system lets you tailor the repairs and maintenance as per the actual wear and tear of the Machine. It does such by allowing you to use a past record of both the parts’ and machines’ lifecycle, resulting in only the required maintenance at the needed time.
High Efficiency At Work:
Not only Machine Monitoring helps you to get an accurate understanding of production, but also it helps eliminate bottlenecks and perfect production schedules. It empowers you with the information that’s required to balance lines and time production runs.
Optimum Inventory & Resource Consumption:
With Machine Monitoring at your side, you have the ability to measure the exact input, output, and energy consumed. This information can further help you enhance your production, refine your manufacturing schedules, and reduce wastage.
No Manual Efforts Required:
Driven by automation and based on advanced technologies like Artificial Intelligence and the Internet Of Things, Machine Monitoring automatically gathers the required data and provides valuable insights to improve the operations. This also saves you from the chaos of manual entries that could both be time-consuming and error-prone.
Personalized Performance Reporting:
Machine Monitoring facilitates you with tailor-made performance reports inclusive of all the important information fetched, compiled, and filtered from multiple sources. This also provides you with sure-shot, concise, and actionable data to expedite the entire analysis process.
Machine Monitoring Is Spread Across How Many Different Branches?
With branches, we mean the various applications or use-cases of Machine Monitoring. Yes! Machine Monitoring is spread across different cases as they comprise everything from monitoring, analysis, industrial sensors to the touch-screen interfaces mounted on machines. Also, not to forget that these systems are interconnected with IIoT or Manufacturing Application platforms.
For Overall Equipment Effectiveness:
If you’re looking for constantly and objectively measuring the state or condition of your Machine, it is Machine Monitoring that could help you precisely. It allows the operators to annotate reason codes for downtime, thereby helping in documenting the root cause at the source. Moreover, machine monitoring systems facilitate you to balance the production lines, track the operations, and plan the production. It also lays a foundation for calculating essential Machine KPIs such as quality, availability, utilization, OEE, etc.
Production Tracking & Job-Route Optimization:
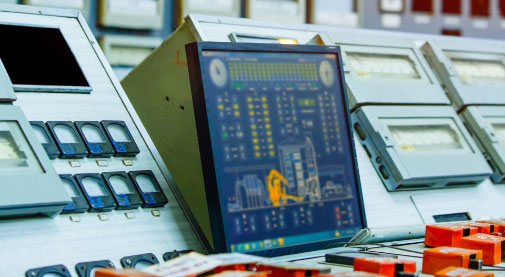
Another use of Machine Monitoring could be found for Production Tracking & Job-Route Optimization. How? You would be wondering… Well, Machine Monitoring brings you the merit of easily tracking WIP throughout the value stream. With the dashboards of Machine Monitoring systems, you can find the exact status of how close a particular run is to completion. It also lends you other valuable insights as well, such as whether or not you are meeting the production quotas. This collectively helps you with Job-Route optimization to gain the maximum benefits from your job.
Condition Monitoring:
Worried about the condition of your machines? Here’s the machine monitoring system to your rescue. It not only helps you track the condition of each of your machines but also provides a complete understanding of part and asset lifecycle. The sensors attached to the system allow you to monitor different essential parameters such as temperature, noise, vibration, etc., and that too in real-time. This way, Machine Monitoring helps you optimize maintenance schedules and decipher machines’ behavior on the shop floor. It stands as an add-on when it comes to establishing a robust foundation of the predictive maintenance programs, provided that the system deals in collecting data about the Machine’s performance and health in the set local conditions.
Resource Monitoring:
One of the intriguing applications of Machine Monitoring is Resource Monitoring. As businesses are focused more towards cost-savings, the requirement of elevating the efficiency of assets; resource consumption. Organizations receive the privilege of easily measuring current, power draw, and other resource usages such as injection wax, coolant, water, etc. This further helps manufacturing units optimize usage, plan inventory and buffers, reduce costs, and more.
Apart from the above-mentioned, Machine Monitoring also finds a place for applications like Program Optimization, Tool Life-Cycle Optimization, and more.
What’s The Way To The Roots Of Machine Monitoring?
Getting started with Machine Monitoring could be a tough task if the proper path and measure are not adopted. Machine monitoring systems could be understood as simple as any software that appends intelligence to the machine data. These systems could be devised in a cloud-based SaaS platform, PaaS platform, or on-premise IT infrastructure of the organization.
Keep Track Of Your Manufacturing Operations:
Firstly, describe your overall operations, as doing this could inform you of the different machine monitoring approaches and solutions. With this step, you gain some hypothesis that for what reason your current manufacturing performance isn’t up to the mark.
Build Initial-Level Hypothesis:
The initial-level hypothesis matters a lot, as it gives you a basic idea of what’s lacking to achieve the set performance. Machine Monitoring has the ability to create new knowledge sources that could further help discover underlying issues. It further stands apt in enhancing clarity to your machining queries by plainly broadening the available information.
Create a Source Of Truth:
Establishing a source of truth could be different for different manufacturing set-ups, but more likely, it could be analyzing the state of the Machine; that’s all about collecting and organizing the relevant data.
Research Evaluation:
This stage brings you the condition of creating tailor-made states of machines that could let you record machine performance to your precise specification. This step allows you to send an automatic trigger notification to a supervisor/technician when certain predetermined thresholds are exceeded.
Educate The Operator:
An essential part comes here…By educating the operators regarding the Machine Monitoring systems, you enable them to use its application for various purposes. They can add details about downtime reasons, logging errors, process completions at source, etc. On the other hand, the application automatically tracks which operator is on duty, the machine program in operation, the number of hours on tools, etc. Hence, providing a holistic understanding of machine health and performance.
Build Tailor-Made Applications:
Yes! Tailor-made applications are a must when you wish to discover the root cause of machine performance issues. If customarily designed, Machine Monitoring systems can help you track quality and production throughout the value stream.
Scale Your Project:
If looking for any of the top-class solutions, then Machine Monitoring stands out to be the one that scales better than other digital alternatives. This is because the solution/system that would work on one Machine could be scaled or transferred to numerous other machines, plants, or even geographies.
The Conclusion
Knowing how machines suit entire manufacturing processes is vital to enhance those processes. Comprehensive machine monitoring solutions that bring machines online and lead operator action to assist you in realizing these developments.
At Teksun, we strive jointly with our clients to devise integrated machine monitoring systems that derive immense value and faster scalability.