The global manufacturing industry is undergoing significant changes. And the Internet of Things (IoT) is driving this change. The Industrial Internet of Things is affecting industrial efficiency as well as identifying smarter methods to work.
Industrial IoT can regulate machine data and transform the new-age manufacturing environment’s processes and systems. Changes in the manufacturing process, supply chain, robotic plants, embedded systems, and networked devices generate real-time operational efficiencies. All of these factors contribute to the reduction of risks while also encouraging innovation. If you’re a manufacturer who ignores IoT solutions, you risk slipping behind your competitors and losing revenue-generating and innovative enterprises.
We discussed how Industrial IoT would affect the industrial industry in this blog. Let’s look at some major points:
Better Maintenance
One of the most important considerations in the manufacturing industry is maintenance. Maintenance is invariably time-consuming and costly. The emergence of Industrial IoT solutions has greatly reduced this problem. IoT allows for improved product and machine efficiency. A single failure in one section of a production machine can wreak havoc on the entire system. Manufacturers would be able to gain more insight into IIoT solutions, and they would be able to go through the data using analytics. Machines can be inspected, and a breakdown can be detected well before it occurs. This will save you a lot of money on maintenance, and you’ll be able to arrange your maintenance time accordingly.
Digitalization
The Industrial Internet of Things (IIoT) allows devices to communicate and exchange data. The Internet of Things (IoT) connects assets to processes, systems, and people in the manufacturing business. This allows for more operational plan integration, increased efficiency, and less mistake. When all of this comes together, manufacturing will reach the next phase of industrial change. For an automated, streamlined, and smart manufacturing process, all of these elements must be integrated.
Flexibility
The ability for businesses to install, operate, and control manufacturing applications from a centralized place has become a reality thanks to the emergence of IIoT and other related technology. Previously, this could only be done by huge industrial enterprises with a larger budget. Any manufacturer, regardless of size or budget, can now participate.
Operational Intelligence
Manufacturers use the most up-to-date operational intelligence to retrieve data from various systems, assets, and people to get 360-degree views of operations, including analyzing data to find root causes to make faster and better business decisions and improve operational performance.
Predictive Analytics
Complexity in the manufacturing industry can be addressed using predictive analytics, which can automatically supply business information to improve overall product quality and transform asset maintenance processes into predictive maintenance before a breakdown occurs.
Scalability
Scalability is one of the most important benefits of IIoT for manufacturers. Manufacturing companies must use a range of software depending on their needs and production goals. On the market, there is a lot of software that can execute various jobs. Manufacturers must comprehend the value proposition. To maximize total productivity while cutting costs, strategic IIoT demands manufacturers to rethink scalable manufacturing and apply it to the manufacturing process.
Cost Optimization
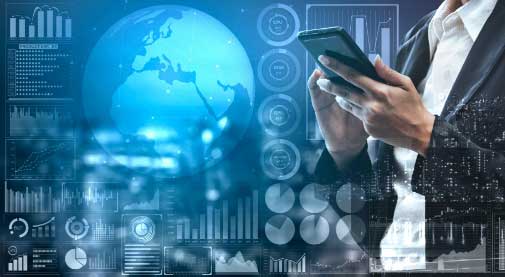
Automated factories will become more productive as the number of low-cost, reliable, and networked sensors grows. Manufacturing equipment and assembly lines may eventually self-diagnose and fix themselves thanks to the Internet of Things. Manufacturing necessitates the use of a large number of perishable tools, which frequently require repair. These tools will not only replace the tooling but will also be connected to the internet of things. It also uses the network to interact with its supplier and place fresh orders.
All of this will result in less downtime, better asset utilization, a cheaper total cost of ownership, a more efficient staff, more actionable performance data, a better final product, and even bigger e-commerce advantages.
Field Service Management
By considering availability, expertise, and location, IIoT solutions can assist firms in determining which field service specialist is most suited for the job. For example, the technician may get detailed problem reports in real-time, ensuring that he arrives at the factory with the right tools and parts.
Future IIoT Applications
Industrial IoT will have the greatest impact on the manufacturing industry. The introduction of IoT will bring $3.9 trillion to the manufacturing sector.
Autonomous Vehicles
By the end of the year, autonomous vehicles are expected to be on the road. These intelligent trucks will aid in reducing the effects of the growing driver shortage while also improving carriers’ safety. Like an electric logging device, the IIoT will promote compliance with regulatory standards at the same time. This will reduce the amount of money owed to manufacturers by the supply chain.
Asset Tracking
The current level and quality of a manufacturing company’s assets determine its value. Manufacturers will be able to track their assets automatically with IIoT-connected devices, which will aid in the development of collaborative relationships with vendors and partners.
Inventory Management
From real-time data to POS transactions, the IIoT helps manufacturers better manage and control inventory levels and customize orders to meet customer demands.
Label Demand Changes in Real-Time
IIoT will enable producers to notice demand fluctuations in real-time. This will aid them in dealing with demand fluctuations. In addition, this will help to improve warehouse management, asset allocation, and supply chain management systems even more.
Single Screen Operator
You can connect assets and ERP systems to provide need-based views via augmented reality experiences or related applications, allowing you to deliver work instructions and quality capture in context, boosting operator productivity and total product quality.
Operational Intelligence
You can now gather, aggregate, analyze, and transmit insights from various assets, operators, and systems into single real-time visibility of KPIs for improved operational performance and sound decision making, thanks to the Internet of Things.
Manufacturing companies are constantly under pressure to cut manufacturing and operational costs, improve consumer reach, and generate long-lasting products. While businesses place a high value on technological benefits, the Internet of Things is becoming increasingly important.
The amount of data collected around the world is growing at a 40 percent annual rate. By 2020, we will have generated 35 zettabytes of data per year—the undiscovered potential of big data, leading to data analytics. By 2020, big data’s untapped potential, which is now dominating data analytics, will be realized. In data management from multiple sources, the industrial IoT will play a key role.
According to business executives, the focus will move from capital expenditures to operating expenses by 2020. Manufacturing organizations will create and retain loyal customer relationships, boost customer lifetime value, control quality standards throughout the manufacturing process, and innovate new goods thanks to the Internet of Things.
Wrapping up
Effective production process management is critical as global market rivalry, and industry changes compel enterprises to rethink their manufacturing operations. To maximize asset usage and efficiency, smart manufacturing necessitates IoT-driven analytics. When manufacturers collect and combine data with analytics-driven insights, they get the flexibility and decision-making power they need to deal with rising market demand and complexity.
The Industrial Internet of Things (IIoT) offers a lot of potential for making production smarter and more efficient. Many manufacturing organizations are changing their dimensions and the way they work due to the Internet of Things. The best methods for tracking, monitoring, and storing supplies are in high demand among manufacturers. As a result, automated tools such as CNC, sensors, and devices generate a large amount of data that can be evaluated, a common IoT use case.
When we look at the whole role of IIoT in manufacturing, we can see that it aids in:
Smart layout design based on consumption statistics.
Quality control for raw materials and finished goods is automated.
Device settings that are intelligent and based on historical data.
Power management, resource management, inventory management, fleet tracking, machine maintenance, and predictive analysis.