- Predictive Maintenance is an excellent strategy that allows companies to keep machinery in good working order before breaking it down.
- Companies can profit from predictive Maintenance since it has a high return on investment, is less expensive than reactive maintenance, and can help reduce repeated expenses.
- Starting small, identifying PdM-ready jobs, and identifying the requisite resources are ideas for implementing a Predictive Maintenance System in your firm.
Regular Maintenance is vital for any firm that relies on complex machinery or devices to function and run smoothly. Those in the manufacturing industry are well aware that if machinery is not maintained regularly, it may break down, resulting in downtime and costly repairs. Preventative Maintenance is the activity of periodically inspecting and tuning up equipment, whether or not it is needed. However, a newly developed technique intends to make Maintenance far more efficient and cost-effective.
What is Predictive Maintenance?
The technique of servicing machines before they break down is known as predictive Maintenance. This is because certain devices may perform better than others. Therefore, organizations may save money on downtime and Maintenance if they know when to tune up equipment rather than sticking to a normal tune-up schedule.
How predictive maintenance works
The internet of things (IoT) sensors used in predictive Maintenance are wirelessly connected to a console that collects and analyses data from the machine. Sensors detect various data fed to a computer, which organizes it and delivers it to you in a usable format. The data produced by IoT sensors can tell you a lot about how a machine is working, from temperature to vibrations and ultrasonic detection.
Vibration sensors detect any small, abnormal changes. Thermic sensors, for example, can tell if particular moving parts have too much friction. Other sensors keep an eye on the amount of oil and lubricant in the system to make sure there’s enough and that it’s clean.
Machine learning dissects the data and contextualizes it in terms of machine performance and wear. Then, using the mountains of data gathered, IoT applications notify you when Maintenance is required, or a breakdown is approaching.
Tips for a Successful Preventive Maintenance Strategy
Predictive Maintenance System practices that are most effective involve a multifaceted approach to addressing possible machinery quality and performance concerns before they emerge. Preventative maintenance ideas are provided below to assist you in tailoring a strategy to avoid unplanned downtime caused by a machine malfunction.
-
Assess the present state
Conducting a baseline assessment of your facility and equipment before beginning any new maintenance plan is always a smart idea. This will provide you with a bird’s-eye view of your facility, which will aid in your decision-making. Consider the quantity, age, and types of machines in your facility, as well as their OEMs, the whole production chain inside your facility, automation level, and any significant previous maintenance concerns, whether one-time or reoccurring. After you’ve considered the big picture, assess the strengths and weaknesses of your current facility and where you’d like to focus on increasing Maintenance and performance.
-
Review manufacturer specifications
After assessing your facilities and machinery, it’s time to start looking into manufacturer specifications. This isn’t the most enjoyable aspect of the procedure (that would be seeing your preventative maintenance plan), but it’s a necessary first step. Manufacturer documentation and specifications can assist you in determining the optimal maintenance methods for your machinery, which will be an important component of your development strategy.
-
Documentation cannot be overstated
Documentation is an essential part of any good maintenance strategy. In general, you’ll want to save as much documentation as possible, including the current state of your facility, your freshly formed maintenance plan, and the activities you take to implement that plan. Comprehensive documentation helps you keep track of the work you’ve done so far, establishes a single dependable resource for the Maintenance practices you implement, and allows staff to readily access and review the plan as you develop your preventative maintenance plan. All of these things will contribute to favorable outcomes.
-
Train and retrain
Without your personnel, your preventative maintenance plan would fail. It’s critical that they can contribute actively and effectively to your facility’s preventive maintenance strategy. Create a specific training program to communicate established PM techniques to give them the tools they need. Make sure it’s not a one-time thing; retraining should happen whenever new procedures are implemented, as well as at regular intervals.
-
Strive for buy-in
Predictive Maintenance System has a negative connotation among facility owners and personnel at times. It can be viewed as a technique that reduces productivity, causes extra labor, and increases unnecessary downtime. Make it clear to your personnel that preventive Maintenance is an integral part of their duties and a key role in the facility’s operation. It boosts overall productivity while also lowering the need for more expensive reactive Maintenance in the future.
-
Set facility goals and benchmarks
Using the big-picture assessment you did in the first point, you can set facility goals for uptime, productivity, quality, and other factors. Comparing incremental improvements to your starting point regularly will help you and your staff stay motivated as you see the benefits of your efforts.
IoT-based Predictive Maintenance
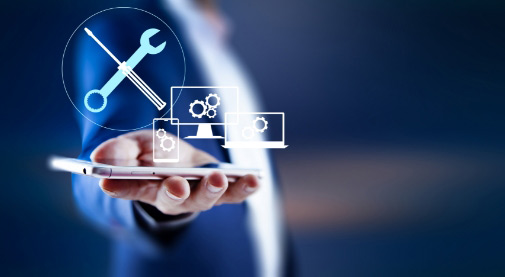
Predictive Maintenance System based on IoT competes with time-based approaches. Some argue that an IoT-based solution is a superior option because mechanism failures are frequently attributed to accidental causes (80%) rather than age (20 percent ). SCADA is a well-known program for maintenance services. However, it only allows for local implementation. In contrast, IoT provides for the storage of terabytes of data and the execution of Machine Learning algorithms on multiple machines simultaneously.
The data from the sensors that the device or equipment is attached to is collected and processed through a series of steps. This is required to reach the end goal, a Predictive Maintenance application that will notify users of probable device and equipment problems. So, let’s look at these transitions in more detail:
The device or equipment with sensors
During this stage, we’ll select the essential values of the equipment we want to monitor (for example, the temperature and voltage of a battery) and arrange sensors to capture them.
Field Gateway
Because data from sensors cannot be sent directly to the Cloud Gateway, a Field Gateway, which filters and processes the data, is added to the chain.
Cloud Gateway
The Field Gateway sends information to the Cloud Gateway, enabling secure transmission and connectivity with various field gateway protocols.
Data Lake
The Data Lake is the next phase, and it speaks for itself. Sensor data is received “raw,” which means it may contain irrelevant or erroneous information. It is represented by a collection of sensor readings taken at a specific point in time. When the data stored here has to be analyzed, it is moved to the Big Data Warehouse.
Data Warehouse
The data is cleaned and structured in this step. It includes the sensor parameters and temporal and contextual information on the types, locations, and dates on which the parameters were measured. It’s now time to integrate it into the Machine Learning model.
Machine Learning model
We can identify hidden dataset relationships, detect anomalous data patterns, and anticipate future failures in the Machine Learning process.
Web/Mobile Application
Finally, using a User Application, we may receive warnings and monitor alerts on future maintenance needs.
Conclusion
Predictive Maintenance System is used in the manufacturing and automotive industries, but it is mostly used in these two. This solution lowers maintenance expenses, minimizes unexpected failures, overhaul, and repair time by over 60%, and dramatically boosts equipment and device uptime. Manufacturing leaders are starting to recognize the value of adopting Predictive Maintenance with Machine Learning to monitor expensive and complicated machines, and industry 4.0 will be dependent on it. While the adoption of Predictive Maintenance is still in its infancy, Teksun provides the proper implementation of the technology.
After reading your article, it reminded me of some things about gate io that I studied before. The content is similar to yours, but your thinking is very special, which gave me a different idea. Thank you. But I still have some questions I want to ask you, I will always pay attention. Thanks.