Market Research Future predicts that by 2022, “the global predictive maintenance market is expected to grow to $6.3 billion”.
Companies in asset-intensive sectors fight to keep a balance between managing costs down and asset availability up. Powerful asset management and maintenance play a pivotal role in assuring that this balance is kept – letting these businesses comply with commands, circumvent the costs connected with additional maintenance, and withdraw unplanned downtime.
What is predictive maintenance?
Predictive maintenance (PdM) manages maintenance to prevent predicted problems rather than managing maintenance on a fixed program or when an issue occurs.
You may have the idea of predictive maintenance but may not be aware of how it is different from your current methods. Let’s try to quickly resolve other maintenance practices and help you in understanding why predictive maintenance is a better alternative.
Designed, preventative, or scheduled maintenance:
The maintenance schedule is fixed and performed at frequent periods. Maintenance exercises are fixed, full control and maintenance of all machine elements is conducted over time. Not all machine components may be reviewed with the same regularity, though. So maybe part A is checked monthly, element B is checked periodically. Though, over time, all fault-prone parts of the machine are reduced.
Condition-based maintenance:
Maintenance is managed as problems occur.Predictive maintenance systems are better than other methods as it lets the business stop problems without additional periodic maintenance. Therefore, some elements may never be checked over a manufacturing facility’s lifetime if they are not predicted to cause difficulties.
How Does Predictive Maintenance Work?
Predictive maintenance is accomplished by assessing the health and performance of devices through cyclic or constant asset condition monitoring. Data carried by IoT devices connecting different assets and systems allow businesses to predict, design and take proactive levels for any events like parts repair or machine failure before it occurs. Predictive maintenance is often performed while the machine is working under normal working circumstances to bypass any interruption in the business.
Is Predictive Maintenance Right For Your Business?
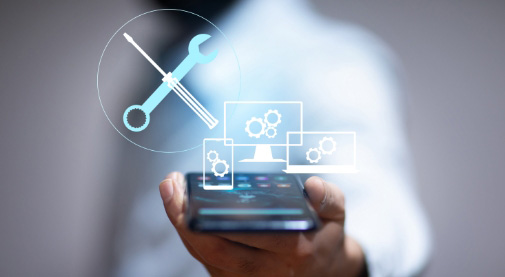
Predictive maintenance needs a huge capital expenditure in technology and labor to perform. If a business does not have many superior facilities or severe health and safety standards, instead of a predictive maintenance program, it should continue a preventive maintenance program. Here are some queries your business should consider before you select to perform a predictive maintenance program:
- What is the estimated cost of our equipment/device?
- Is it important for our device?
- What has the machine record been like thus far?
- What do our reports show about equipment downtime, injuries, losses, and safety warnings?
- What kind of predictive maintenance machine would be most suitable for our business’s requirements?
- Is my business financially ready to spend on predictive maintenance technologies or specialists at this time?
- These are only a few ideas to think about before you choose to move ahead in implementing predictive maintenance in your company..
What are the Benefits of Predictive Maintenance?
As per the PWC report, on average, predictive maintenance in industries could:
- Decrease costs by 12%
- Increase uptime by 9%
- Overcome safety, wellness, environmental, and quality risks by 14%
- Increase the existence of an aging asset by 20%
Funds spent only on required examinations, renovations, or component replacement (no guesswork)
predictive maintenance examines and recommends these measures just before any significant loss or machine downtime occurs.
Predictive maintenance sets your company working like a well-oiled machine with fewer or no lost-time events due to surprise breakdowns and reactive maintenance improvements.
Maximized machine lifespan due to needed repairs and maintenance
predictive maintenance assists in stopping any real equipment damage from happening, so you can have relaxation about the functionality of your assets.
Improved revenue
predictive maintenance, while it may be expensive upfront, could cease saving your business major dollars down the line by preserving your most important equipment.
What are the costs of Predictive Maintenance?
While improved by using sensors mounted on machinery, the advantages of predictive maintenance can be performed using portable multimeters that various maintenance areas already own. The software required to make this type of maintenance is more cost-effective than ever. The frequency of machine downtime is reduced because the predictive maintenance used real-time condition data. The system will automatically create a work order once the asset data shows a potential issue and inform the proper technicians to complete the work. This approach saves businesses money by decreasing downtime and labor costs since assets are repaired when the system sees a potential problem.
What is the Size of companies using predictive maintenance?
A long ago, predictive maintenance was only available for giant companies with high budgets. However, the software and technology connected with PdM have become budget-friendly for almost any size company that needs to be as proactive as potential with maintenance work.
What to consider before implementing PdM
Before implementing a predictive maintenance system, to justify the investments, every business should have a clear business case. Businesses with various machinery crucial to services, such as manufacturing or healthcare, must maintain assets working for as long as possible. Manage the price of machine downtime for your company and determine whether predictive maintenance is the best way to stop that.
Bottom Line
Inspecting industry beyond predictive maintenance, foretellers are studying toward determined rather than predictive maintenance. Prescriptive maintenance strives for a fully automated approach. It practices machine-to-machine (M2M) methods to enable machines to schedule maintenance for themselves.
Though, manufacturers with valuable equipment might, at least initially, want the possibility of human input. So, to completely take the power of digital transformation, businesses must look end-to-end for technical solutions that are human-compatible and match with emerging business and technologies trends.
The journey to perform predictive maintenance does not just need proper data management. In complicated system integration, there is also a requirement for flexible platforms that draw together the complete range of data experts, tools, systems, microservices, and ultimately, recognize for ideal human-data interaction.
In conclusion, a predictive maintenance system is remodeling manufacturing. Feel free to connect with our team, who would assist you in understanding the best maintenance method to your facility’s particular requirements, or schedule a demo to know how our Predictive Maintenance module works in practice.