What is a Digital Factory?
A digital factory is a manufacturing plant in which humans, equipment, raw materials, and finished goods exchange data about the production process in real-time. Smart sensors, nominal cloud computing, and Big Data analytics are included, and it incorporates data and information from previously separated IT and operating systems.
The IoT factory automation uses technologies to transmit data digitally through the entire operation, including data from both materials and computers. A coherent infrastructure involving simulation technology, connected equipment, and collaboration resources is needed for digital manufacturing.
There are a few different technologies and features that digital factories migrate, and manufacturers who incorporate several technologies are more likely to be labeled as “digital factories.” In a digital factory, you might encounter the following technologies:
Industrial Internet of Things
Tiny sensors and other hardware are linked and communicate with one another in the IIoT. Even though there is an almost infinite number of use cases for IIoT solution in manufacturing, they could be used for asset management, energy reduction through smart HVAC and lighting, or system data collection.
Industry 4.0 and the Internet of Things (IoT) are vital components of the technology transition since they represent smart, integrated equipment and goods that communicate and optimize themselves through the entire supply chain.
5G
5G has been designed to meet the needs of commercial IoT and is a catalyst for modern industrial transformation. The industry 4.0 solution is about to be expanded by 5G technologies, which will allow much more speed, versatility, cost efficiency, and efficiency. It’s the next step in the digital transition. 5G promises greater bandwidth, reduced latency, and quicker speeds.
- The same computer would be able to do various tasks thanks to rapid remote reprogramming.
- Production line robots can also be streamlined remotely and with less time.
- Machine learning and AI can be applied at unprecedented speeds thanks to real-time connectivity.
Machine Learning and Predictive Analytics
Machine learning and predictive analytics are two examples of applications for the gathered data in engineering and other sectors. Data can be combined and used to power machine learning models that offer decision-making information from collections of data that are often too difficult for humans to understand on their own.
Machine learning and predictive analytics can be used to forecast demand, perform predictive and Prescriptive Maintenance on computers, and identify business prospects, among other things.
Predictive analytics ensures that a manufacturer’s equipment is in good working order and helps keep the whole plant on track. A manager will be safe, ensuring that the equipment would not break down unexpectedly in the middle of a manufacturing run if it is calibrated to a high degree of precision. One of the advantages of a digital factory is this.
Automation
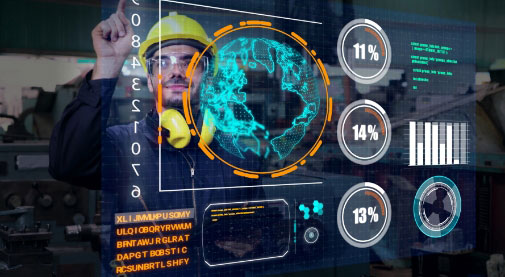
With the advancement of smart, wired robots, humans would step out of the loop and allow automation to take over. Machines are more capable of managing tasks faster and more accurately than their human counterparts in many ways.
Industrial robotics frees up these people’s time to focus on more nuanced thinking problems that are better suited to human brains than computer minds.
Few automated factories use lights-out production processes to push robotics to the next stage, totally removing humans from the manufacturing chain. The automation principle stems from the opportunity to start a factory, switch off the lights, and walk away with the impression that the factory can continue to produce without human intervention, even 24 hours a day.
Edge Computing Technology
Cloud technology allows automated factories to store and monitor large amounts of data using protected equipment shared with others and accessible through the internet.
Manufacturers will benefit from cloud-based applications for data management and stability, as well as for analytics capabilities.
Smart manufacturing generates a large amount of data, which necessitates a large amount of storage.
Local computing solutions can be challenging to come by, and cloud providers can be costly. Data storage at the edge is a perfect compromise. Edge computing takes data from the factory floor and processes it locally, avoiding the time it takes to send data to the cloud, track it, and re-assign it to the factory floor. Edge computing is suitable for safety mechanisms, Prescriptive Maintenance, and other time-sensitive computing activities because it enables real-time analytics and fast decision-making using data.
What Are the Advantages of a Digital Factory for Business?
One of the significant benefits of a digital factory is a substantial increase in productivity.
Even if many factory workers are concerned that the rise of robotics and other emerging technology will force them out of work, digital manufacturing opens up a slew of new, higher-paying careers that many people find more stimulating and rewarding.
These higher-paying positions often entice young people, who bring new ideas, experiences, and concepts to the table to improve the facility.
Similarly, robotic factories are erecting a barrier to creativity. Because of the versatility built into the infrastructure by real-time analytics, there is a lot of room to innovate, be innovative, find solutions to emerging business challenges, and test strategies at scale without wasting energy.
Customers are more satisfied with digital factories because prices are lower, delivery times are shorter, and efficiency and accuracy are higher.
Digital factories generate robust and real-time data, which improves performance, productivity, protection, and environmental compliance. It also enhances production workflow management and the movement of everything from raw materials to work-in-progress and finished products. It also provides administrators with near-real-time access to organizational data, allowing them to resolve roadblocks and inefficiencies quickly.
Bottom Line
IIoT solution in Smart manufacturing aids in streamlining corporate processes, increasing efficiency, and increasing return on investment. The scope for smart manufacturing is enormous, and security concerns need not be a deterrent. When it comes to building or modernizing smart factories, industry leaders must establish confidence.