To be competitive in today’s industry, Talking lightning speed producers must be quick in all aspects of their activities. This desire for speed, combined with advances in IoT technology, has spurred a new manufacturing movement: the industrial internet of things (IIoT).
The Industrial IoT is the next generation of Internet of Things technologies, and it is remarkable in that its implementation has changed manufacturing. Companies seeking a strategic edge today should consider the capabilities that IIoT provides – the advantages impact everything from maintenance to retailer logistics, staff workflows, and product distribution.
To begin, you must first comprehend industrial IoT and how it is changing manufacturing processes.
What is Industrial IoT (IIoT)?
IoT technologies are used worldwide, and they allow all of the integrated gadgets we use, such as wearable technologies and virtual assistants. Then, the Industrial Internet of Things is taking the global interconnectivity we’ve come to rely on and extending it to large production facilities. The risks are higher, but the rewards are greater.
Since Industry 4.0 is completely customer-centric, suppliers would have to bring in extra work to provide priceless customer experiences and facilities. Brand visioning, product sales, sourcing, assembling, and service management are all part of the customer-centric business 4.0.
IoT makes this step simple by assisting the owner in staying current with the customer’s ever-changing desires and preferences.
The Internet of Things (IoT) and Business 4.0 are undergoing significant changes.
IoT is to credit for industry 4.0’s lightning-fast evolution, in which everything is wired to a shared network and processes are largely automated, obviating the need for any human interaction. Real-time data analysis increases decision-making, and predictability reduces the likelihood of potential risks in the field and asset protection for future workability. The main stages of IoT and industry 4.0 evolution are:
- Getting things connected
- Generating insights
- Optimizing operations and processes
- Innovation
Benefits of IIoT
By 2025, the global industrial IoT market is expected to reach 933.62 billion dollars.
So, what do today’s industrial IoT systems give manufacturers? Here are five of the most significant advantages of implementing a completely connected IIoT production process.
Increase efficiency
- The most significant advantage of IIoT is that it allows manufacturers to simplify and improve their operational performance. Robotics and automatic machines can increase efficiency and help factories streamline their processes by working more effectively and reliably.
- Physical machinery can also be linked to software through sensors that continuously track results. Manufacturers can have a greater understanding of the operating efficiency of particular pieces of machinery and whole fleets due to this.
- IIoT-enabled data systems allow manufacturers to increase operational efficiencies.
- Bypassing manual activities and functions in favor of automatic, digital ones,
- Making data-driven choices in all aspects of production
- Output can be monitored from anywhere, whether it’s on the factory floor or thousands of miles away.
Errors Can Be Reduced
- The Industrial Internet of Things enables factories to digitize almost every aspect of their operations. Manufacturers can reduce the greatest risk associated with manual labor – human error – by reducing manual procedures and entries.
- This is more than simply a matter of technical and production errors. Human error-related cyber and data attacks can also be reduced with IIoT solutions. People are the leading cause of cybersecurity attacks, according to a Data Security Trend survey, with human error accounting for 37% of all breaches.AI and machine learning-enabled programs and devices will do all of the requisite computation on their own, removing the possibility of anyone making a basic error and jeopardizing the manufacturer’s data.
Predictive Maintenance
- Machine downtime has the most detrimental effect on a production process. According to Aberdeen Research Group, the total cost per hour of downtime in all production forms is $260,000. What may be causing such severe problems that factories are unable to function? The solution is straightforward: there is a lack of adequate and proactive maintenance.
- When maintenance is reactive rather than constructive in the industrial environment, factories are left trying to figure out what’s wrong, how to fix it, and how much it’ll cost. All of these problems are solved with predictive maintenance powered by industrial IoT solutions.
- Manufacturers may establish a benchmark by regularly monitoring machinery efficiency and operation. This baseline, along with the data that goes with it, gives businesses the tools they need to spot problems before they happen. They should then plan repairs ahead of time to avoid downtime, which helps them in the following ways:
- Have all of the necessary components on hand for the job.
- You will prepare for the project if you know how much it would cost ahead of time.
- Shift manufacturing to a certain location of the factory to avoid affecting commodity quotas.
- Ascertain that the equipment is performing at its best.
Improve Safety
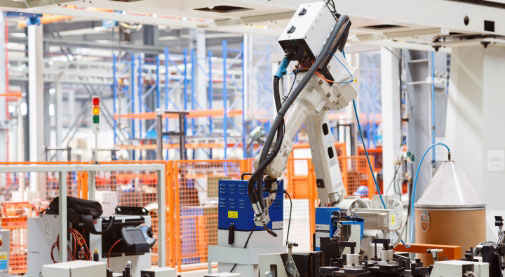
- All of the data and sensors that a fully functional IIoT manufacturing operation needs are also helping to improve occupational safety. When all Industrial IoT sensors work together to track workplace and employee safety, “smart manufacturing” becomes “smart defense.”
- Staff on the floor, on the line, and in delivery are all protected by integrated protection systems. If an injury happens, everybody in the factory will be notified, processes will be halted, and corporate leadership will be able to interfere to ensure that the accident and incident are handled. This incident can also yield useful information that can be used to deter a recurrence in the future.
- Wearable technology is a newer solution that some manufacturers are implementing for their workers. Wearables have been a part of the Internet of Things since its inception, but they are only now finding their way into commercial IoT operations.
- Wearables assist leaders with keeping track of factors like employee posture and ambient noise levels, which can also enhance working environments and perhaps improve performance. Employees may also be notified if they are not meeting proper occupational safety protocols, allowing them to correct their conduct and remain safe on the job.
Cost-cutting
- Awareness is a strength, and IIoT solutions provide producers with the resources they need to cut costs and increase sales. Data-driven insights into operations, development, marketing, and revenue, among other areas, will help companies succeed.
- Predictive management, fewer mistakes, better quality management, and increased efficiencies are all advantages of Industrial IoT that can increase a company’s earnings. Industrial IoT also provides the most useful platform for production executives: perspectives from everywhere, at any moment.
- Manufacturing activities can now be monitored remotely 365 days a year, 24 hours a day, seven days a week, from anywhere in the world. This 360-degree view of the entire production chain, as well as the after-sales support offered to consumers, are invaluable tools.
Teksun: Your Partner for all IoT based industrial solutions
Whether it is Agritech, Security & Surveillance, Health Care, Drones & Autonomy, and Automotive, almost every industry can complete IoT-based smart systems to enhance their productivity with decreased cost. Teksun is one of the most prominent companies that provide end-to-end IoT solutions. The company’s strongest feature is that it does not restrict its offerings to a specific industry; rather, it gives IoT-based smart technologies for all sectors. Teksun is contributing 100% of its resources to the fourth industrial revolution. Sensors, gateways, dashboards, and software are the core components of the company’s IoT systems, working and tracking under extreme conditions. The company’s sensor devices come with all of the required functionality and provide useful information.
Conclusion
The Industrial IoT has drastically altered our perceptions of things in the workplace. At a rapid rate, capitalists are becoming more interested in advanced methods. The Internet of Things is making a huge contribution to making businesses smarter and improving workflows. Teksun, a manufacturer of end-to-end IoT solutions, takes the lead by, among other things, making the system robust and handy. The organization is focusing on adding groundbreaking features to its products to improve process performance greatly.