In a ‘just-in-time’ production climate, unplanned failure in just one machine will cause delays, resulting in dissatisfied buyers, potential consumer turnover to a rival, and a direct hit to a company’s bottom line.
Machine data can be used to reduce the cost and effect of scheduled and unplanned downtime, which is one of the genuinely great consequences of the development of industrial IoT (Internet of Things). Predictive maintenance is another term for this.
What is predictive maintenance?
Predictive maintenance, or PdM for short, is a tool for predicting the need for maintenance in factory equipment. Patterns arise from observing operational data from the units, enabling operators to anticipate what maintenance is expected on any particular device, allowing it to be scheduled at less expensive periods.
Manufacturers focused on preventive repair, also known as the “if it ain’t broke, don’t repair it” approach. You can understand that just repairing computers as they broke down was a massive expense, both in terms of unplanned maintenance and the possible effect on other parts of the machine and the production quality at the period the component was failing.
To diagnose future issues, predictive maintenance uses precise data extracted from each machine. Vibration analysis is one example. A model that uses a baseline of captured system performance data may predict variations, including a rise in vibration in a particular component, which may be caused by damage or the presence of a foreign object.
What are the benefits of predictive maintenance?
The benefits of a predictive maintenance system cannot be overstated in terms of cost savings!
- Optimizing planned downtime
- Minimizing unplanned downtime
- Optimizing equipment lifetime
- Optimizing employee productivity
- Increasing revenue
We’ll go into each of these one by one.
Predictive maintenance assists in optimizing planned downtime.
Planned downtime will include anything from washing and lubricating machines to replacing components that are known to malfunction frequently. Preventive maintenance like this lowers the chances of unplanned downtime. You’ll get more efficient and better-quality output from a well-serviced machine, much as you’ll get more efficient and better-quality output from sweeping your computer for bugs or keeping other appliances tidy in your device.
Preventive maintenance systems should be scheduled daily and at periods that would have the least effect on order output, thanks to data gathered during system operations. There’s also the bonus of proper servicing extending the life of a computer that would otherwise be impossible and expensive to repair. Maximizing part uptime and life would eventually pay off in significant cost savings.
Predictive maintenance limits unplanned downtime
“Unplanned downtime costs manufacturing factories an extra $50 billion annually,” according to a Wall Street Journal report. In intensely efficient production markets, using predictive maintenance to reduce costs is important.
Monitoring devices digitally gather reams of data that, when analyzed, can reveal trends on any particular machine, so routine proactive maintenance will ensure that machines operate most of the time smoothly. Based on historical records, this type of pattern recognition can help predict a system expected to suffer an outage and for which repair can be scheduled ahead of time.
Preventive maintenance systems can help to optimize equipment lifetime.
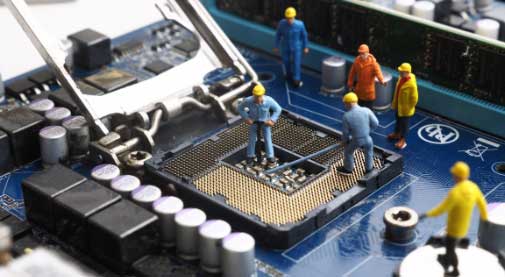
Monitoring a machine’s performance, production, and consistency over time can reveal data that will help determine when a machine needs maintenance and when it is nearing the end of its life, as mentioned above.
The maintenance plan can change as computers age and their frequency of usage changes, controlled by predictive maintenance. Over time, various parts of the system can respond to output stress in different ways. When a system reaches a turning point in terms of expense vs. efficiency, the resulting rise in maintenance expected by data trends will show.
The ability to predict and prepare for the potential need to repair major sections of a system, or the whole device, makes it manageable from a cost/budget and time / effort standpoint.
Preventive maintenance systems can help optimize employee productivity
Predictive maintenance improves workforce morale in a variety of respects. Let’s start with the labor cost: as repairs are planned, the time required for maintenance is shortened due to a limited number of part replacements rather than complete equipment replacement.
Additionally, the level of equipment critical breakdown repairs will be limited, as will the number of “critical callouts.”
Reduced breakdowns and crash prevention devices, which can warn or even stop machines when a worker is in danger, can greatly increase factory conditions and eliminate worker accidents from the employee’s viewpoint.
Additionally, downtimes and operations with sub-optimal parameters have an effect not only on performance but also on employee morale. Rushing to tackle challenges as they emerge is exhausting. Predictive management reduces the likelihood of such occurrences.
Preventive maintenance systems can help increase revenue.
The benefits of predictive maintenance we’ve discussed so far all have the same goal: to improve the bottom line. Repairs can be handled more easily with less maintenance on good components and faster replacement of defective components, minimizing repair time.
McKinsey performed one of the most detailed analyses on the promise of industrial analytics like predictive maintenance in 2015, and they discovered the following improvements:
- Maintenance expenses are reduced by 10% to 40%: Since scheduled maintenance is dependent on a timeline, there will be times that activities are completed that aren’t needed. Such inefficiencies may be avoided with predictive maintenance.
- Maintenance costs are cut by ten percent to forty percent: Since routine maintenance is time-bound, there will be periods when operations are performed that aren’t needed. Predictive management can help you prevent inefficiencies like this.
- New prospects for development have been discovered in the range of 10% to 50%: Advanced analytics will uncover new perspectives on process management opportunities every day until data processing is automated.
How to implement predictive maintenance
Now that it’s obvious that Preventive maintenance systems is a surefire way to prevent unplanned downtime and higher production costs, the next issue is how to put one in place.
- First, get to the heart of the issue you’re trying to solve:
- Is unplanned downtime more important to you than the expense of a component failure?
- Are there any machines on your floor that are more relevant than others? i.e., more commonly used, central to more instructions, and so on…
Then you must evaluate your current situation or establish a baseline of system output data. You should use your guidelines, OEE standards, or other business standards to do this. Examine each machine’s previous output levels, such as how long it has been down, which modules malfunction often, and how often maintenance is currently planned, among other things.
Second, look for trends in the historical data to determine which measurements will signify a concern and which deviations from the baseline can warn an operator.
Bottom Line
Finally, after using these trends and statistics concerning the reference success metrics, you’ll need to set up a system for updating and checking the data regularly and ensuring that it accurately reflects the actual situation and flags any worsening patterns that indicate a need for maintenance. This is crucial: you can’t guess something you haven’t looked at. It’s important to have accurate records!
Minimizing unplanned maintenance, at least when it applies to system operation, saves a lot of money and prevents shortages in getting products to market, which hurts the bottom line. Preventive maintenance systems are no longer ‘good to have’ in today’s industrial world. It’s a must.